Oxygen Analyzers in Chemical Reaction Control: Precision, Safety, and Process Optimization
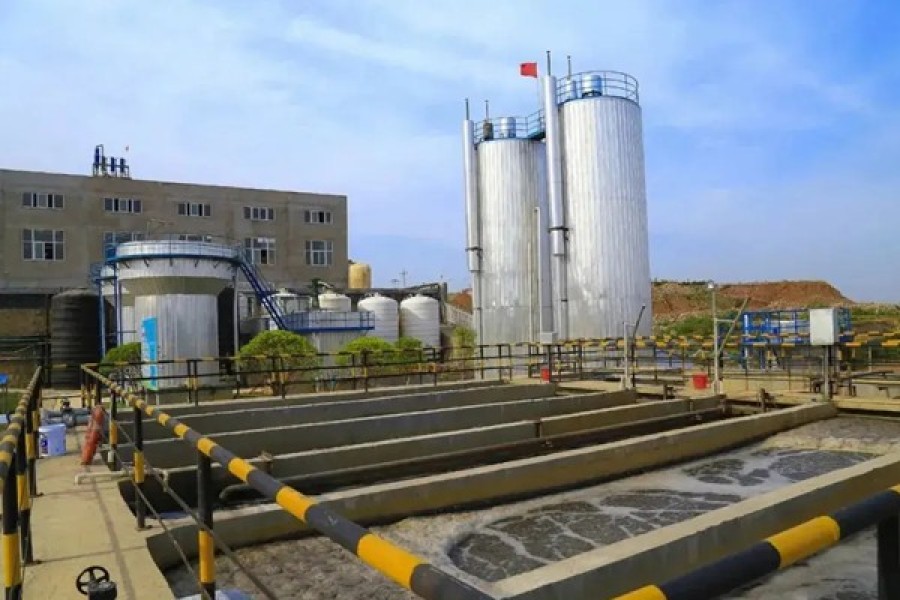
By John Doe - 31/03/2025 - 0 comments
In the chemical manufacturing industry, maintaining precise oxygen levels during reactions is critical for product quality, safety, and sustainability. Oxygen analyzers play a vital role in monitoring and regulating oxygen concentrations in real time, ensuring optimal process conditions while mitigating risks of explosions, unwanted side reactions, or energy waste. Let’s delve into how these instruments drive efficiency and innovation in chemical processing.
Why Oxygen Matters in Chemical Reactions
Oxygen’s presence or absence directly impacts reaction pathways, reaction rates, and final product properties. For example:
♦ Oxidation Reactions: Controlled oxygen levels are essential in producing chemicals like sulfuric acid (via contact process) or ethylene oxide (a precursor for plastics).
♦ Inert Atmospheres: Many reactions, such as hydrogenation or polymerization, require low-oxygen environments to prevent degradation or explosive hazards.
♦ Bioprocesses: In fermentation or enzymatic reactions, oxygen levels dictate microbial activity and yield.
Uncontrolled oxygen can lead to catastrophic failures (e.g., runaway reactions) or financial losses due to off-spec products. Oxygen analyzers act as the first line of defense, enabling dynamic adjustments to maintain equilibrium.
Key Applications in Chemical Reactors
1. Exothermic/Endothermic Reactions
In reactors handling exothermic processes (e.g., nitration reactions), excess oxygen can accelerate combustion or trigger thermal runaway. Analyzers ensure oxygen stays within safe thresholds, preventing accidents and improving energy efficiency.
2. Catalytic Processes
Catalysts like platinum or palladium in ammonia synthesis or methanol production require specific oxygen concentrations to function effectively. Deviations can poison catalysts or reduce yields.
3. Polymer Production
In polyethylene or PVC manufacturing, oxygen can cause chain termination or discoloration. Real-time monitoring prevents defects and ensures polymer consistency.
4. Environmental Compliance
Oxygen analyzers track exhaust gases to verify compliance with emission standards (e.g., VOC recovery in petrochemical plants).
Types of Oxygen Analyzers for Chemical Reactors
1. Electrochemical Sensors
Cost-effective and widely used, these sensors measure oxygen partial pressure via oxidation-reduction reactions. Ideal for low-risk environments like storage tanks or pipelines.
2. Zirconia-based Analyzers
Robust and precise, zirconia sensors operate at high temperatures (600–1000°C), making them suitable for harsh reactor conditions. They excel in high-pressure systems, such as steam methane reformers.
3. Infrared (IR) Spectrometers
Non-contact IR analyzers detect oxygen in gaseous streams without sample extraction. They are ideal for explosive or reactive environments, such as ammonia synthesis loops.
4. Paramagnetic Analyzers
Leveraging oxygen’s magnetic properties, these devices offer high accuracy for ultra-pure applications, such as semiconductor-grade chemical production.
Case Study: Preventing Runaway Reactions
A specialty chemical manufacturer producing adipic acid faced recurring safety incidents due to uncontrolled oxygen ingress during nitric acid oxidation. After installing **zirconia oxygen analyzers** in their reactors, they achieved:
♦ 98% reduction in safety incidents by maintaining <1% O₂ levels.
♦ 15% higher yield through stabilized reaction kinetics.
♦ $2.8M/year savings from avoided shutdowns and waste.
Challenges and Solutions
♦ Corrosive Environments: In chlorine or sulfuric acid plants, sensors degrade rapidly. *Solution*: Use inert materials like Hastelloy®-clad sensors.
♦ High Humidity: Moisture interferes with IR analyzers. *Solution*: Integrate sample gas dryers.
♦ Low Concentration Detection: Trace oxygen in inert atmospheres demands high sensitivity. *Solution*: Laser-based analyzers with ppm-level precision.
Future Trends: Smart Integration
The rise of Industry 4.0 is transforming oxygen analyzer applications:
♦ Predictive Maintenance: AI algorithms predict sensor failures before they occur.
♦ Digital Twins: Simulate reactor behavior to optimize oxygen setpoints in real time.
♦ IoT Connectivity: Remote monitoring enables global teams to respond instantly to deviations.
Conclusion
In chemical manufacturing, oxygen is both a friend and a foe. Oxygen analyzers empower operators to harness its benefits—enhancing reaction efficiency, product quality, and cost savings—while neutralizing its risks. As processes grow more complex and sustainability demands intensify, these instruments will remain central to safe, efficient, and innovative chemical production.
For engineers and plant managers, investing in advanced oxygen analyzers isn’t just about compliance; it’s about future-proofing operations in an industry where precision can mean the difference between profit and peril. The molecule that powers life must be mastered to power progress.