Oxygen Analyzers in In-Pack Gas Monitoring: Preserving Quality, Safety, and Shelf Life
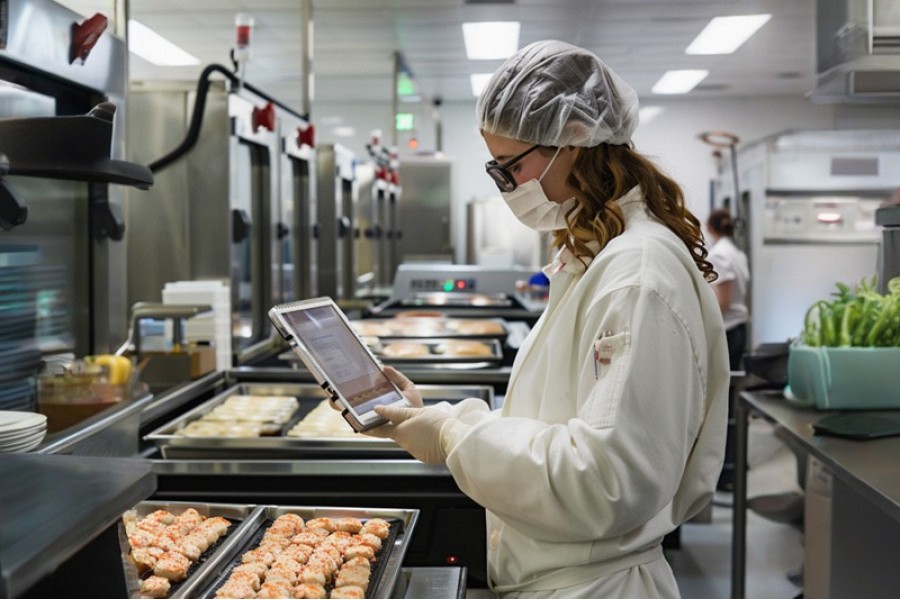
By John Doe - 31/03/2025 - 0 comments
In the competitive world of consumer goods, packaging is not just about aesthetics—it’s a critical barrier against contamination, spoilage, and oxidation. Oxygen, while essential for life, can be a nemesis in sealed environments, accelerating rancidity in snacks, corrosion in metals, or degradation of pharmaceuticals. Oxygen analyzers have emerged as indispensable tools in monitoring and controlling in-pack gas composition, ensuring products remain fresh, safe, and compliant with global standards. Let’s uncover how these technologies are revolutionizing packaging across industries.
Why Monitor Oxygen Inside Packages?
Most packaging relies on modified atmosphere packaging (MAP) to extend shelf life. By replacing air (21% O₂) with nitrogen, carbon dioxide, or other gases, manufacturers slow oxidation and microbial growth. Oxygen analyzers play a pivotal role in:
♦ Quality Control: Verifying oxygen levels are within target ranges (e.g., <1% in snack bags or <0.1% in sterile medical vials).
♦ Leak Detection: Identifying compromised seals that allow oxygen ingress, compromising product integrity.
♦ Process Optimization: Ensuring gas flushing during packaging meets specifications, reducing waste.
Without precise oxygen monitoring, even minor deviations can lead to costly recalls, consumer dissatisfaction, or regulatory penalties.
Key Applications Across Industries
1. Food and Beverage Packaging
♦ Snack Foods: Nitrogen flushing in potato chip bags prevents staleness. Oxygen analyzers validate flush efficiency.
♦ Dairy and Meat: Modified atmospheres with low O₂ inhibit bacteria like *Clostridium botulinum* in vacuum-sealed products.
♦ Beverages: Monitoring dissolved oxygen in beer or wine packaging to prevent oxidation flavors.
2. Pharmaceuticals
♦ Blister Packs: Maintaining inert atmospheres protects sensitive tablets from moisture and oxidation.
♦ Vials and Ampoules: Ultra-low oxygen levels (<100 ppm) are critical for biologics and injectables to avoid degradation.
3. Electronics and Industrial Packaging
♦ Semiconductors: Inert gases like nitrogen prevent oxidation during IC component packaging.
♦ Metal Parts: Vacuum or nitrogen purging avoids corrosion in precision components.
Technologies for In-Pack Oxygen Analysis
1. Electrochemical Sensors
♦ How They Work: Measure oxygen partial pressure via oxidation-reduction reactions.
♦ Use Cases: Portable handheld devices for quick checks of sealed packages in warehouses or on production lines.
2. Optical Sensors (TDLAS)
♦ How They Work: Tunable Diode Laser Absorption Spectroscopy detects oxygen in gas mixtures without sample extraction.
♦ Use Cases: Real-time monitoring in automated MAP systems for high-speed food packaging.
3. Gas Chromatography (GC) with O₂ Detectors
♦ How They Work: Separates gas components and quantifies oxygen in complex mixtures.
Use Cases: Lab-based analysis of prototype packaging designs or regulatory compliance testing.
4. Paramagnetic Sensors
♦ How They Work: Leverage oxygen’s magnetic properties for high-accuracy measurements.
♦ Use Cases: Critical environments like sterile pharmaceutical filling lines.
Case Study: Extending Shelf Life in Premium Coffee
A leading coffee roaster implemented **in-line oxygen analyzers** in their nitrogen-flushing packaging line. Before adoption, inconsistent gas flushing led to inconsistent shelf life and customer complaints about stale flavors. With real-time O₂ monitoring:
- Oxygen levels reduced from 8% to <0.5%, extending freshness from 3 weeks to 6 months.
- Energy costs dropped by 12% due to optimized nitrogen usage.
- Recall risks eliminated, boosting brand reputation and repeat purchases.
Challenges and Solutions
♦ Packaging Material Interference: High-barrier films can block sensor access. *Solution*: Use non-invasive optical analyzers or integrated inline sensors.
♦ Low Oxygen Detection Limits: Trace oxygen in pharmaceutical packaging demands ppm-level precision. *Solution*: Combine GC with laser-based analyzers.
♦ Cost of High-End Equipment: Budget constraints in SMEs. *Solution*: Deploy portable analyzers for periodic checks instead of continuous monitoring.
Future Trends: Smart Packaging Integration
The convergence of oxygen analyzers with IoT and sustainability goals is reshaping the field:
♦ Smart Labels: Disposable O₂ indicators embedded in packaging change color if oxygen breaches thresholds, aiding consumers and retailers.
♦ Predictive Maintenance: AI analyzes sensor data to predict gas flushing system failures before they occur.
♦ Circular Economy Alignment: Recyclable packaging materials paired with analyzers reduce waste and resource use.
Conclusion
Oxygen analyzers are the silent guardians of modern packaging, ensuring that the air inside sealed containers is as controlled as the products they protect. From keeping your morning cereal crisp to safeguarding life-saving medicines, these technologies bridge the gap between innovation and reliability. As consumer demand for fresh, safe, and sustainable products grows, in-pack oxygen monitoring will remain a cornerstone of packaging excellence. For producers, the message is clear: mastering oxygen means mastering quality—and the future of packaging is being written one breath of fresh air at a time.