The Role of Oxygen Analyzers in Steelmaking: Enhancing Efficiency and Sustainability
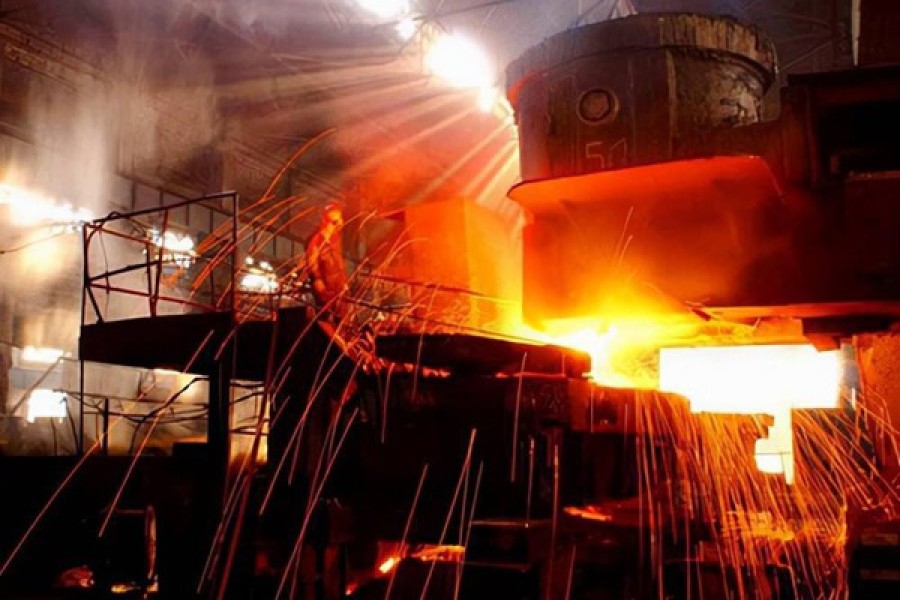
By John Doe - 31/03/2025 - 0 comments
In the highly competitive and environmentally conscious steel industry, optimizing every step of the production process is critical. One technology playing a pivotal role in achieving these goals is the oxygen analyzer. By providing real-time insights into oxygen levels during steelmaking, these instruments directly impact product quality, energy efficiency, and carbon footprint reduction. Let’s explore how oxygen analyzers have become indispensable in modern steel production.
The Science Behind Steelmaking and Oxygen Control
Steel production revolves around precise chemical reactions, particularly oxidation and reduction processes. In basic oxygen furnaces (BOF), electric arc furnaces (EAF), and secondary refining units like converters, controlling oxygen content is crucial:
♦ Decarburization: Removing carbon from molten iron requires controlled oxygen injection.
♦ Slag Formation: Proper oxygen levels ensure efficient removal of impurities such as phosphorus and sulfur.
♦ Temperature Management: Excess oxygen can lead to unintended heat loss or unstable reactions.
Oxygen analyzers act as the "eyes" of the furnace, enabling operators to maintain optimal conditions dynamically.
Types of Oxygen Analyzers in Steel Mills
Modern steel plants deploy two primary types of oxygen measurement technologies:
1. Zirconia-based Oxygen Analyzers
Using zirconium dioxide sensors, these devices measure partial pressure of oxygen in gases (e.g., flue gas). When heated above 650°C, zirconia becomes conductive, with conductivity proportional to oxygen concentration. Installed in exhaust systems, they provide immediate feedback on combustion efficiency and help adjust airflow to minimize fuel waste.
2. Laser Spectroscopy (TDLAS)
Tunable Diode Laser Absorption Spectroscopy offers non-invasive, in-situ analysis of gaseous oxygen. This method excels in harsh environments, delivering millisecond-response data for rapid process adjustments. It also reduces maintenance costs compared to extractive sampling systems.
Applications That Drive Value
♦ Blowing Control in BOFs: Oxygen purity and flow rates are fine-tuned based on analyzer readings, ensuring consistent steel chemistry while cutting excess oxygen use by up to 15%.
♦ Emission Compliance: Real-time monitoring of off-gas oxygen helps enforce environmental regulations by minimizing CO and particulate emissions.
♦ Energy Savings: By balancing oxygen input with fuel consumption, mills reduce gas usage—a critical factor as energy prices fluctuate globally.
♦ Quality Assurance: Consistent oxygen levels prevent defects like hydrogen-induced cracking or inclusions in finished products.
Case Study: Reducing Costs by 12%
A Japanese integrated steelmaker implemented zirconia analyzers across three BOF converters. Within six months, they achieved:
- 8% reduction in scrap metal usage due to better process control.
- 12% lower oxygen consumption through optimized lance positioning.
- Improved energy recovery in waste heat boilers, saving $2.3 million annually.
The Road Ahead: Smart Integration
With Industry 4.0 advancements, oxygen analyzers now integrate with AI-driven control systems. Predictive analytics forecast optimal oxygen schedules, while digital twins simulate process variables for preemptive adjustments. Future innovations may include miniaturized fiber-optic sensors for localized measurements in molten metal baths.
Conclusion
In an era demanding both operational excellence and sustainability, oxygen analyzers stand out as unsung heroes of steelmaking. They bridge the gap between traditional metallurgy and smart manufacturing, proving that even the oldest industries can embrace cutting-edge innovation. As decarbonization targets tighten, these devices will remain central to building a greener, leaner steel sector.
Whether you’re a process engineer seeking technical insights or a plant manager aiming to future-proof operations, understanding oxygen analyzer applications is no longer optional—it’s essential. The future of steel is measured in parts per million—and beyond.